Sea Otter Classic | 9 new mountain bikes from Salsa, Pinarello, Specialized, Digit, Trek and Liv
Our pick of the new MTBs at the California show
The best cycling kit bags | Five bags to carry your gear to rides and races
Get your riding gear in order with these versatile carry-alls
Review | DT Swiss ER1400 Dicut wheelset
A premium-performing, progressive alloy wheelset
How to service the hubs on your bike
Service your wheel bearings for a smoother ride
Canyon releases Neuron:ONfly – its first lightweight electric mountain bike
Lightest Canyon eMTB yet uses Bosch’s SX motor to help it fly up climbs
First ride review | Canyon Neuron:ONfly CF9
Does Canyon’s Neuron:ONfly give a glimpse of the future of electric bikes?
Privateer 141 ditches internal cable routing and gains mullet compatibility
Privateer's second-generation 141 arrives for testing
A do-it-all adventure shoe: 6 key features of the Northwave Hammer Plus
Introducing Northwave's all-rounder off-road shoe
Review | Assos Equipe RS Rain Jacket Targa
Premium weather protection for a premium price
Tech Q&A | Drivetrain lifespan, derailleur drama and road bike touring mounting woes
Your questions answered by the experts
How to measure bolt circle diameters – and why cranks use different BCDs
Crankset BCD demystified
Review | Fox Dropframe Pro helmet
The latest Dropframe helmet offers plenty of coverage and impressive ventilation
New Look 785 Huez switches to a threaded bottom bracket and uses nanotube tech to reduce weight
Size medium frame claimed to weigh 985g
Sea Otter Classic | 12 new road bikes from Blackheart, FiftyOne, Van Rysel, Haro, ENVE, BMC, Giant, Canyon and more
The best new road and gravel bikes from the 2024 Sea Otter Classic in California
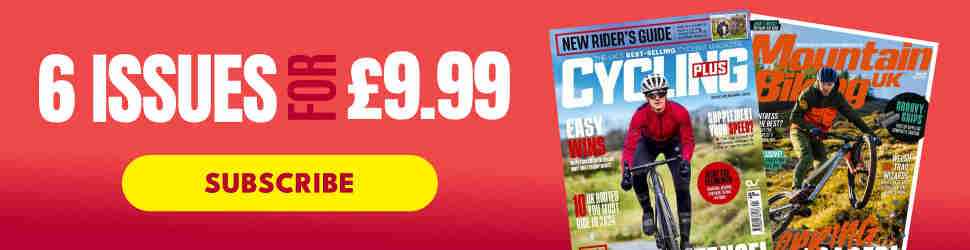
Editor's Highlights
Light bikes, mismatched kit and more – road tech the pros can't have, but you can
Due to the UCI and team sponsors, you have more choice than the pros
New Saracen Myst is fastest yet with 211mm of rear travel and low-slung rear shock
Downhill bike's full frame redesign results in lower centre of gravity
Schmolke’s new carbon parts will transform your Brompton into a weight-weenie commuter
German lightweight specialist targets weight-focused commuters with folding bike parts range
Listen to the BikeRadar Podcast
Latest Reviews
Review | Specialized S-Works Torch Lace shoes
There's knot a lot wrong with Specialized's premium lace-ups
Review | KS Vantage dropper post
Dropper seatpost promising premium operation at a lower price point
Review | Shimano GE9 shoes
Can Shimano’s do-it-all enduro and gravity shoe do it all?
Review | Ornot Ecopak bar bag
Review | PNW Loam Dropper Post
PNW’s Loam Dropper offers good performance and plenty of adjustability
Review | Chris King ARD44 wheelset
Performance carbon wheels, but perhaps not as you know them
Best Products
14 of the best road bike tyres: our favourite tubeless and clincher tyres
The best tyres for racing, training and more…
Best cycling gilets 2024 | 8 windproof vests to protect you from the elements
Eight vests to keep the wind and showers out
What are cycling cameras and why should you own one?
We break down the uses and options for this popular accessory
Best endurance road bikes in 2024: our pick of the best bikes for speed and comfort
What to look for in an endurance road bike and our pick of the best
Best road bike wheels in 2024 | 30 rim and disc brake wheelsets tried and tested
The best wheels for road cycling
26 of the best trail bikes tested by BikeRadar
The top trail bikes as rated by our expert reviewers, plus our buyer's guide for everything you need to know
Advice
13 leg workouts for cyclists – and why you should do them
Follow these easy exercises to build up your leg strength on the bike
How to fit, remove and change bike pedals
We talk you through how to fit and remove your bike pedals in this clear step-by-step guide for beginners
How to repair a punctured tubeless tyre
Tubeless technology has revolutionised the way we ride, both on and off-road, but it’s not totally foolproof
The best backpacks for commuting and urban riding
The best backpacks for commuting and urban cycling in 2024
Bike components explained: a jargon buster for all of the key frame, wheelset and groupset parts on a bicycle
Get your head around headsets, drivetrains, derailleurs and more
Why do my knees hurt? Cycling knee pain explained and how to manage it
How to identify and treat specific overuse knee conditions for cyclists