We’ve come across a patent from DT Swiss that promises an advanced magnetorheological (MR) damping fluid based suspension that can be adjusted electronically and in real-time while riding to control the damping characteristics as desired.
- Top 5 future bike technologies we'd like to see
- The ultimate guide to mountain bike rear suspension systems
There’s been a lot of interesting suspension development this year. DT Swiss released its F535 ONE suspension fork with variable, travel-dependent damping and we’ve also had a ride on Fox’s new Live Valve system, which controls compression valves electronically, but we think that the patent we've found may be a glimpse into the future of suspension design.
Rheological-what now?
MR fluid consists of magnetic particles suspended in a carrier oil. When a magnetic field is applied, the particles align themselves along the field lines, increasing the apparent viscosity of the fluid.

Image courtesy of Wikimedia Creative Commons Will Becker
The strength of the magnetic flux allows the yield stress of the fluid to be precisely controlled. Put this in a valve system, and the stronger the magnetic field, the higher the resistance of the MR fluid to flow will be.
This means that rather than control suspension damping with valves and shim stacks, it can be modified by adjusting the magnetic field to the desired strength.
Sounds easy, so what’s the problem?
MR fluid exhibits some unusual properties when a magnetic field is applied.
When activated by the magnetic field, the MR fluid actually behaves similarly to a solid until its yield stress (which is set by the strength of the magnetic field) is reached. At this point, the MR fluid can begin to flow through the damping valve.
This means that at a given magnetic field strength, the suspension will first have to overcome a ‘breakaway’ force before the suspension is able to compress.
DT Swiss mentions past incarnations of suspension where this leads to an on-off feeling in the suspension performance, with poor sensitivity of the shock as the flow of the MR Fluid is restricted until the breakaway force is overcome.
What does DT do differently?
A key part of the idea proposed by DT Swiss is a control method intended to reduce or completely eliminate the breakaway force described above. In turn, this control method also lowers the power requirements of the system.
To do this, the viscosity of the MR fluid is modulated proportionally to the force transmitted through the suspension. This allows the shock to be operated above the breakaway force of the MR fluid at all times.
Think of it this way; before any input to the suspension, it is static, and there is no need to increase the damping. With no magnetic field applied, the MR Fluid simply behaves like a normal fluid and can flow without a breakaway force having to be overcome.
Force has to be applied for the suspension to start moving through its travel. As soon as this happens a shear stress acts on the MR fluid and its viscosity can be adjusted to a level where the shear stress acting on the fluid is always above the breakaway force described previously.
With continuous modulation of the magnetic field strength, the shear stress experienced by the MR fluid is always above the breakaway force — avoiding the “on-off” feeling previously described.
Custom damping curves
This dynamic control concept can be extended with real-time tuning of the suspension while riding. The adjustable viscosity of the MR fluid means that it is also possible to adjust damping curves as desired.
This means a characteristic damping curve can be defined, which adjusts the damping depending on the shaft speed of the shock.
Uniquely, the damping curve can be adjusted to have any characteristics or profile desired and is not limited by the physical constraints of valves or shim stacks.

All aspects of the damping can be controlled independently. The magnetic field is simply adjusted in strength to modulate the damping force according to the requirements.
This means that the damper curve is dynamically generated in real time, by setting the magnetic field strength to adjust the MR fluid to the corresponding damping force required.
There are various exciting ways in which this could be extended, with different damping curves for different terrain, conditions or suspension states.
The key point is that the damping is not dependent on mechanical valves and instead is electronically controlled, essentially providing infinite flexibility in how it is controlled.
On the fly suspension tuning
In order to achieve this real-time suspension tuning, the suspension must be capable of monitoring itself.
That requires a controller with a regular update cycle which is able to monitor the speed and position of the suspension shaft, determine the correct damping rate and modulate the magnetic field acting on the MR Fluid.
DT Swiss suggests using a position encoder or accelerometer to determine the speed the shaft is moving at as well as it’s position within the suspension stroke — well-proven technology that shouldn’t be too hard to implement.
In the patent, DT Swiss describes that response times for a bicycle damper need to occur within 10 or 20 ms for a smooth riding experience.
We can’t see a huge problem with calculation speed for such a system. MR fluid is also able to react quickly to magnetic fields, with a response time of less than 1ms, allowing it to adapt quickly to the damping force required.

The limiting factor will likely be the response time of the magnetic field but DT claims that response times of 10 ms have been achieved with a prototype already.
Save energy, keep control
An additional requirement for such a system the power needed to generate the magnetic field (and run the control system). The higher the damping required, the higher the power needed to energise the electromagnet.
Because the suspension system can actively get information on its own state, DT claims that it is able to minimise the energy used, by only energising the magnetic coils when the suspension experiences an external input.
Even then, the highest current input will rarely be used as large shocks are the least frequently experienced.
This allows the system to modulate the power requirements in real time, energising the fluid enough to provide sufficient damping whilst using the minimum overall amount of energy.
This is key to conserving battery power. Rather than setting a damping force which requires constant power input, the control system can modulate the power input and requires little to no power when the suspension is not active.
How this plays out in real life in terms of battery life remains to be seen though. We are unclear how much power is actually needed to control the MR fluid adequately.
DT Swiss also suggests that the suspension could be configured with a baseline damping curve that is tuned, as in a traditional shock, with the fluid flow through valves.

This would allow the shock to be used without power, exhibiting a damping curve that is soft but still rideable. DT Swiss suggests that this could be used as an emergency setting if you run out of power out on the trail.
It may also be possible to incorporate an adjustable valve into the design in order to adjust the base damping manually. This could allow you to adjust the base damping for more aggressive riding or alternatively stiffen up the suspension if you run out of power whilst riding.
Look where you’re riding
An additional interesting feature that could be implemented as part of this system is a machine learning controller to help identify the kind of terrain you are riding on and adjust the shock accordingly.
In addition, DT envisages a scenario where the fork and shock are able to communicate, allowing the shock to anticipate how it should control its damping level best to absorb the shocks from the terrain.
We also imagine that this electronic control scheme would also make it significantly easier for manufacturers (and users) to create custom suspension tunes for their bikes without having to experiment with shim stacks and valving inside the suspension.
What would a magnetorheological suspension system look like?
We actually assume that the design would be quite similar to existing suspension components.
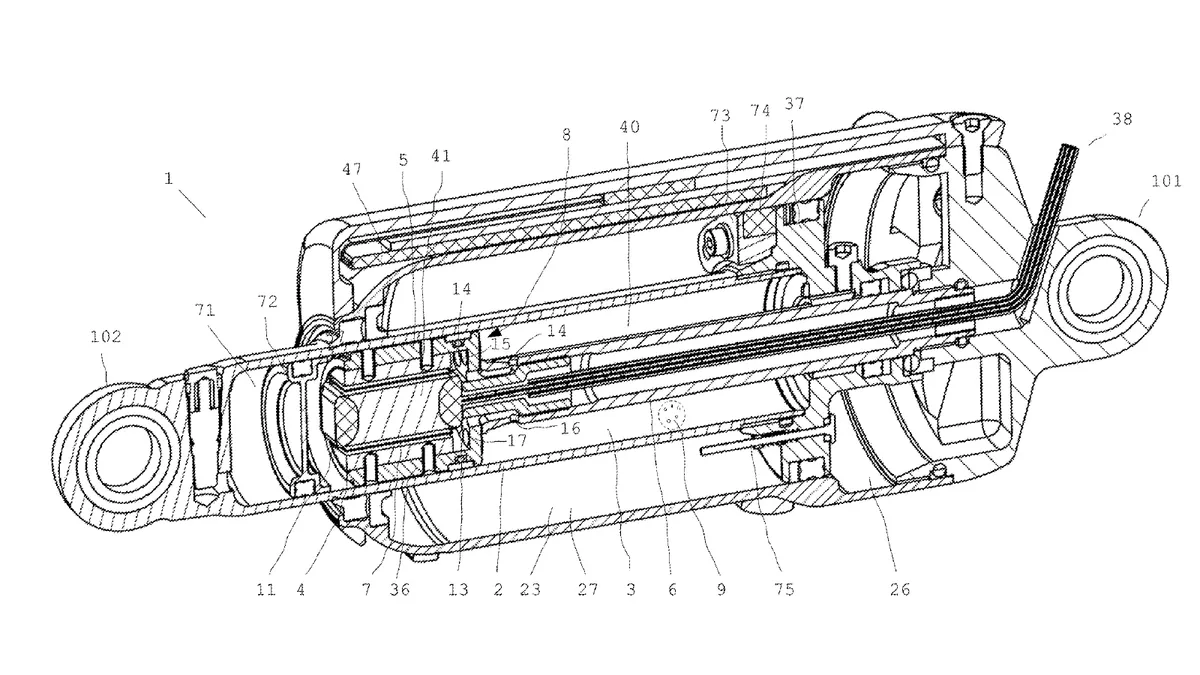
The main difference is that the valving requirements would likely be much simpler because the damping fluid flow is controlled electronically. This obviates the need for shim stacks to control the damping characteristics.
That said, the patent outlines some valving, which restricts the fluid flow on the rebound, presumably to tune the 'baseline' curve of the damper.
Of course, the MR fluid would require an electromagnet to be fitted along with a power supply, but the shock described in the DT Swiss patent does this rather neatly, by placing it inside the piston.
The key component in the system would be the MR valve. This needs to be tuned to match the characteristics of the MR fluid as well as the forces generated within the suspension components.

The patent suggests the main oil path consists of channels between 0.5 to 0.9mm in height. We believe that modifying the channel height is required to ensure the shear stress is high enough to ensure the MR fluid operates above the breakaway force in the normal range of operation.
The properties of MR fluids are complicated to describe, but as a general rule, the smaller the channel, the higher the shear stress experienced by the fluid for a given fluid velocity. However, going into more detail is outside the scope of this article.

Multiple “damping ducts” can be combined to allow for a higher flow rate depending on the damping fluid used, the damping requirements and the range of damping required.
Tuning of the channel dimensions and number allows for matching of the mechanical system to the electronic controls.
For feedback to the control unit, the shock is fitted with a position encoder on the shaft that allows both the position and speed of the shaft in the suspension stroke to be determined. DT suggests an accelerometer could be used too.
When will it exist?
The patent describes a working unit that has been tested out in the field, so the technology is certainly feasible to put together.
It is difficult to speculate about cost — while the internals of the shock largely follows the template of existing designs, the control software would likely require significant work and testing in order to put into practice.
Defining characteristic damping curves that are suited to a wide range of riders, and translating these into appropriate control algorithms for the complex characteristics of MR fluid would likely represent a large proportion of the development of this system.
We certainly see this system as feasible given that a working prototype has been tested by DT Swiss. It also seems like a natural progression to further improve suspension control. We’ll just have to wait and see whether it turns into reality.