Tacx is now the world leader in indoor trainers, and they’ve come a long way from their humble beginnings in 1957 as a bicycle/moped shop with founder Koos Tacx at the helm. Originally the company began producing moped exhausts to expand the business and launched its first bicycle rollers back in 1972. Tacx and his family (three generations now work at the Tacx factory) believe in producing as much as they can in house, and in collaboration with production partners sourced within a 20km radius of the factory (printing, painting, electronic PCB boards) — it’s easy to see Tacx as very much a local operation.
- Tacx Neo 2T Smart review
- Tacx Neo trainer update lets you experience different road surfaces
- Zwift adds massive mountain to virtual reality course
Tacx invited BikeRadar to take a tour of its facility in Wassenaar, Holland with the opportunity to look inside the production processes for Tacx's hugely popular Neo trainer, and get a sneak-peek at the new Flux smart trainer.
First we met with production development engineer Ramon van der Stel who told us a bit about the factory: "Our production development time is vastly reduced compared to most because we have in-house design, development, and manufacturing and we even produce all of our [production] tools too, and with more than 350 moulding tools that’s a lot of production development work."
We asked Ramon how that benefits us the consumers, and he said "A good example is the Tacx Neo, it's been a huge success for us but we haven’t stopped developing and improving it; road patterning ride simulation is a big step and that’s a simple firmware upgrade.
It's expensive to do all of this here, but we think that the quality we are able to produce makes it worth it
"But we’ve also altered the case design slightly as we had feedback from one of our pro teams [Lotto Jumbo] where they found that the [Bianchi] TT bike they used fouled the case because of its narrow chainstays. We redesigned the panel, prototyped it and now have introduced it into the Neo all within a matter of weeks.
"It also means we can change other things, like our Deva bottle cage that was used in the Omloop het Nieuwsblad [a one-day cycling race in Belgium], and two of our sponsored riders said they lost bottles so between this race and E3 Prijs Harelbeke we stiffened up the structure [by adding a layer of carbon fibre] and tweaked the angle that meets the neck of the bottle. We haven’t had anymore negative reports, even from the Tour of Flanders where you’d expect to lose bottles!"
The factory floor

Next we hit the factory floor to see everything in action and meet Edwin Vreeswijk from Tacx’s tooling workshop. Edwin and his team are tasked with maintaining over 350 tools and myriad of machines — Tacx is highly automated, with a lot of processes handled by robots. Once a design is approved, and the production team has specified the tooling, Vreeswijk and his dozen strong team machine tool and refine and feedback to the designers.
Vreeswijk tells us that by handling this all in-house, with engineers that are familiar with the products, they can get to full production far quicker and more accurately than companies who rely on outside toolmakers. "It's expensive to do all of this here, but we think that the quality we are able to produce makes it worth it." Tacx’s workforce is 120 strong, a large number of this staff are highly trained engineers and production management.
Tacx claims a wattage accuracy of 2 percent for the Neo’s power measurement, and the unit we saw tested hit 0.25 percent accuracy
Tacx has for decades believed in automating as much of the manual production process as possible so as we navigate the factory you're more likely to see robots and engineers with laptops and clipboards than factory floor workers.
The bottle production process for instance is pretty much robot controlled from start to finish, it's only the custom line that is operated by people using the injection mould machines and printers,. That’s because a run of custom bottles can be as little as 300 units, so rapid changes in spec and finish are pretty constant.
The fully computer controlled bottle production system can run 24/7 if needed, and manager Edwin Vrauwdeunt (who was one of Holland's top track riders, and at 50 still places highly in the Dutch Derny Championships) talked us through production: "All the bottles we produce are biodegradable and we source only the best bio-granulates for this, we have three fully automated bottle machines all capable of making 365 bottles per hour, 24 hours a day.
"The waste from the bottle productions is taken straight to our automated grinders where it's recycled into material that then goes into making further bottles, or pieces for our trainers – like the feet or casings for levers."

Wattage accuracy
The factory splits production between the entry-level and high-end trainers 50/50. The Neo’s production uses a combination of robotics and people and Vreeswijk explains that "there are a lot of quality checks that need to be done in every step, the internal parts of the Neo are very complex and each piece needs to be perfect before it moves on".
The quality control checks at the final stages of each newly built Neo are impressive. A computer controlled torque sensor and systems analytics were custom built for Tacx's Smart trainers and we watched as a newly assembled Neo was put through its paces.
Tacx claims a wattage accuracy of 2 percent for the Neo’s power measurement, and the unit we saw tested hit 0.25 percent accuracy. Martin Smits, Head of product development, said "the 0.25% reading is what we are seeing most often, so we are talking about refining our information to say the Neo is accurate to within 1 percent. No other trainer on the market, and very few power meters, can get close to that so we are very proud of the Neo’s performance."
Neo improvements

Smits also explained that the way Tacx works means they can look for continuous improvements, and because of the Neo's electromagnetic operation it can be improved without the worry of wear to moving parts acting on each other.
We also got to try out the Flux in a late prototype stage (it still had 3D printed covers and panels), and it keeps the same low-noise character of the Neo
"We’ve also tuned the power mode so it's now faster at the set point. The inertia level of 125kg would be very difficult to get with a mechanical system, you’d need a very heavy flywheel. And road patterning has been interesting because we can alter the resistance up to 1,000 times a second, so we were able to create resistance patterns that simulate cobbles, gravel, ice, wooden bridges, brick surfaces and more," explains Smits.
This all sounds somewhat fanciful, but Smits has a working version set up and ready to go and a few minutes spent running through the surface profiles feels remarkably natural.
We even get a chance to ride a section of the Tour of Flanders with a smooth tarmac climb that then peaks and drops into a section of cobbles, before starting to rise again. The way in which the resistance rises and falls with the topography but also bumps, knocks and shakes with the road surface is freakishly good.
The Flux trainer: or budget Neo
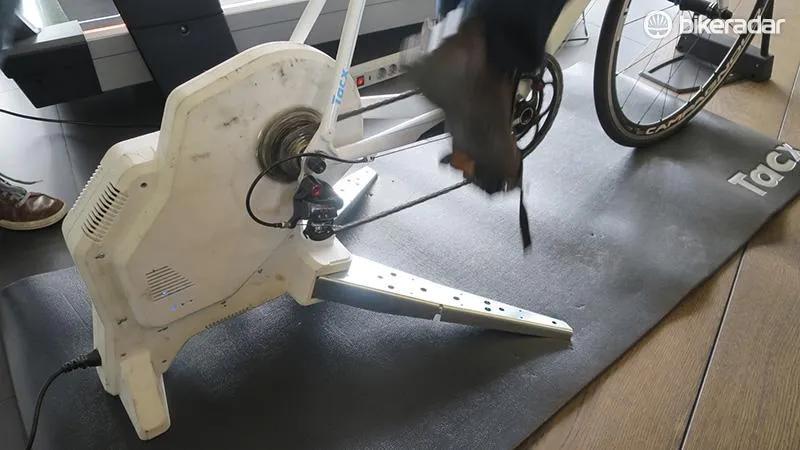
The realistic pedaling, simplicity of use and quiet operation that you get from the Neo trainer are all well and good, but the £1,200 price tag puts it out of reach from your average home-trainer. Tacx is aware of this and has been working on a new direct-drive smart trainer, the Flux.
Tacx’s take on the Ass-Saver style guard is a neat piece of design too
The Flux uses a combination of electromagnetic resistance and a flywheel — using less expensive magnetic coils to keep the price down. The Flux closely matches the Neo in its inertia figures (that value is usually in kgm2 (squared), which Tacx prefers as it is more accurate, so that’s the simulated mass compared to body weight which is usually in kg. So at 125kg it can handle all shapes and sizes), along with power measurement accuracy that’s close at 5 percent.
The 6.7kg flywheel has a simulated mass of 25kg, and it can simulate up to a 10 percent slope and is Ant+, FE-C, and BT (FE-C) compatible with simulated sensors for Ant+ and Bluetooth.
We also got to try out the Flux in a late prototype stage (it still had 3D printed covers and panels), and it keeps the same low-noise character of the Neo. Riding one of Tacx's own virtual routes we found that the pedal stroke feels natural and the simulation is up there with the Neo, although it doesn't have the Neo’s unique road patterning feature. The Flux is however set to retail at a much lower price point of £699.
Tacx accessories

Tacx also showed us its latest range of tools and accessories. The new ‘Tools to go’ range comprises a selection of multi-tools, which includes a compact mini chaintool at £17.99, a mid-size mini Allen set at £15.99, and a mini Allen set with chain tool at £23.99.
The quality is good and the smooth covered design makes them very pocket friendly. Tacx’s take on the Ass-Saver style guard is a neat piece of design too. The seat clamp fitting is universal so you can add a Go-Pro mount, or saddle pack (which weirdly sits underneath the guard), and it’s a rock solid construction. At £14.99 for the guard and £19.99 for the saddlepack (available in two sizes) they look like decent value too.
The carbon/polyamide Deva cage we saw earlier is priced at £11.99, and Tacx’s new twist-lock bottle with a Camelback-style rubberised drink valve is a bargain at £4.99.
We expect more news from Tacx at Eurobike, and will bring your more details on the Flux when we have it — and get to try out the final version.