While common wisdom in the bike business says all cost-competitive frames are built in Asia, the Allied Cycle Works brand has another vision. How about handmade-in-America carbon frames built with innovative technologies, specced with Shimano Ultegra and selling for $4,000?
- Will Trump and Brexit change the bikes we ride?
- 10 entirely convincing reasons to buy a new bike
- The best bike shop in the world
Industry veteran Tony Karklins, who founded Orbea USA, has assembled an all-star cast in the unlikely state of Arkansas to build high-end frames, paint and build them to a rider's preference, and ship the bikes to a rider's door or to a shop. HIA Velo is the parent company behind the Allied Cycle Works brand, which is launching its first bike, the Alfa, this week.
Karklins has the support of co-founder Douglas Zell (Intelligentsia Coffee founder), Sam Pickman (11 years in Specialized's senior engineering team) , Chris Meertens (former Specialized senior composites engineer), Olivier Lavigueur (11 years composite work at Guru) and Jim Cunningham (40 years premium paint experience and founder of CyclArt, which HIA Velo bought).
"We are putting every single part of the process under one roof in the United States," Karklins told BikeRadar. "The business model couldn’t afford to outsource anything. We are bringing in paint, talent, testing, after-sales service, even our tooling manufacturing is in the state of Arkansas."

"We are in the industry, where, if we are honest, nobody makes anything anymore," he said. "When I got into the bike industry in the early eighties, everybody made their own stuff, product was unique and bike shops were cultural hubs. Now there is little passion; it is all about global logistics."
We hope we will be introducing a new paint job every Friday — because we can
While there are certainly a number of smaller, boutique brands that build bikes in the US, often custom or semi-custom, the prices are significantly higher than bikes from the major brands. Karklins says that Allied "certainly respects the artisans, but we are not trying to make the next $15,000 bike. We want to compete with the big three and be price competitive and equally if not higher on technology."
By bringing everything in house, Allied can run just-in time inventory, building bikes to order. Contrast that with the typical industry model of brands asking retailers for pre-season orders and then the brand placing an order with a factory in Asia along with its best forecasting guess as to what will sell well and when.
Allied has six frame sizes, with two head-tube heights possible in each. The customer can pick their component group — including lengths and widths of cranks, stem and bars — wheels, saddle and, notably, the paint job.

"There will be a ton of paint options," Karklins said. "We hope we will be introducing a new paint job every Friday — because we can."
Karklins said the company will offer a lifetime warranty on the frame, as well as repair services "that you can only do if you have production here."
One of the reasons I left Specialized was that I realized that the next thing was going to be around manufacturing processes
"Since we will have the same technicians, using the same materials with the same tools, we can repair a bike without the voiding warranty," he said. "Things like the bike falling over and cracking a seatstay. We can fix that for a couple hundred bucks — and then offer you a deal on a new paint job."
Unique Alfa features
The Alfa is a claimed 875g frame with an English threaded bottom bracket.
Allied is using a new-to-the-bike-world material called Innegra, which is sandwiched into the carbon layup and which greatly increases resistance to failure. Allied showed BikeRadar samples of the material, laid up between carbon. When the carbon on both sides breaks, the flexible Innegra holds it all together.
Innegra is a polypropylene fiber and the company is based in Greenville, South Carolina.
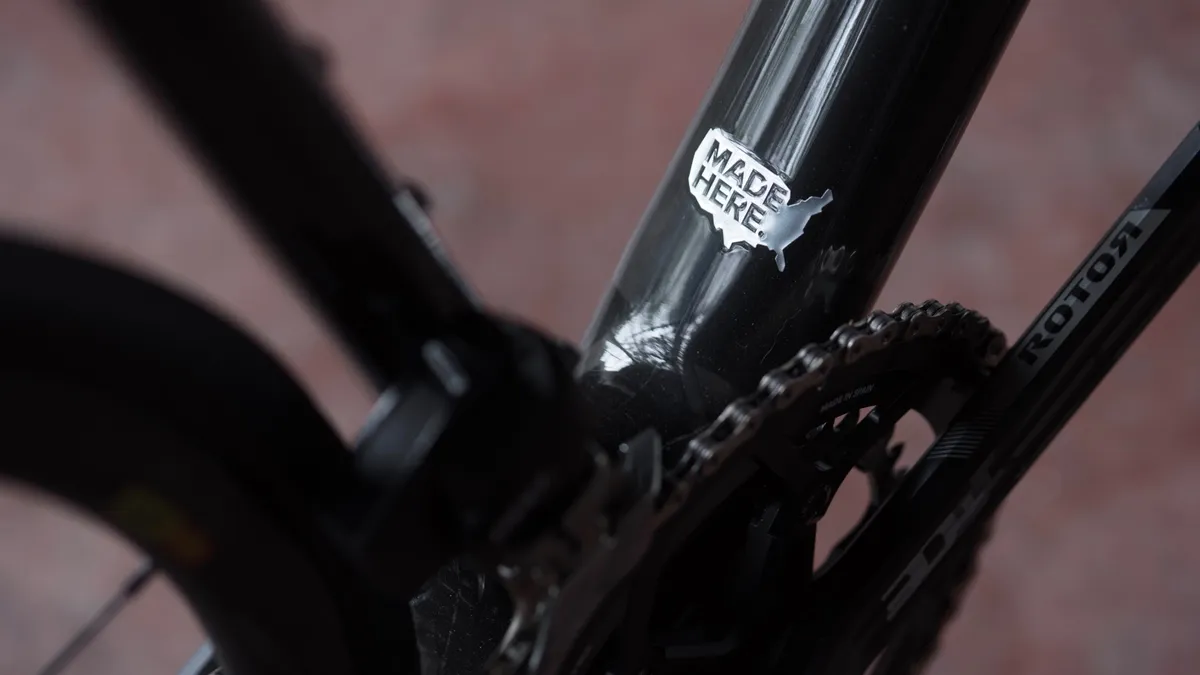
“Say you have a crash and you don’t realize you’ve cracked your regular carbon frame, so you continue to ride it home,” Pickman said. “That can lead to catastrophic failure. With Innegra, even cracked carbon is held together. Also, it changes the bike’s vibration characteristics through the bike and absorbs small impacts through the bike.”
Allied is using Innegra in the top tube, seatstays and fork.
At Specialized, Pickman was the lead R&D manager on the current Roubaix with the FutureShock front suspension. He was also responsible for the recent iterations of the Tarmac, among other projects.
"One of the reasons I left Specialized was that I realized that the next thing was going to be around manufacturing processes," Pickman said. "You weren’t going to be able to do anything truly unique until you held your own manufacturing. You can have a great idea, but unless you have the means to execute, well, good luck. The big brands are all buying from one of five factories. They are using the same tools, the same stuff, the same everything. What it’s forced is this race of features. Some of them do a decent job of improving ride quality, but some of them don’t really do anything but just make things more complicated than they need to be. By owning our own factory, we can do stuff that is truly unique."
You can learn more at Allied's website.