Specialized Bicycles kicked off their global launch for 2012 bicycles and components with a brief tour of their Morgan Hill, California headquarters. The corporate base serves several functions, besides being where the company is run.
It's home to frame, component and helmet development and testing labs; prototype manufacturing for carbon development and alloy components; a full-scale model concept store; SBCU (Specialized Bicycle Components University) for dealer, rep and staff training; and Specialized’s own 1,000 sq ft museum, which serves to greet visitors.
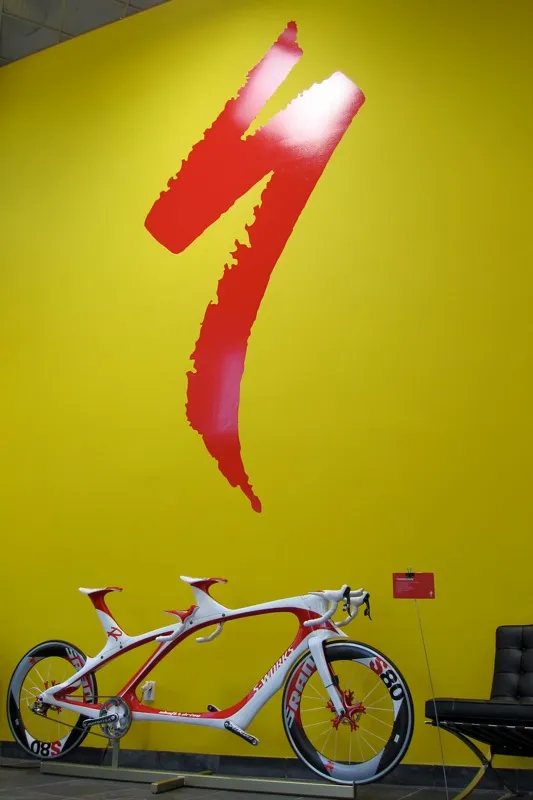
The carbon Shiv tandem concept bike is currently greeting visitors
The coming season will mark the company's 38th model year and the 30th anniversary of the Stumpjumper mountain bike. Gabe Sullens, SBCU’s founding instructor who now works for Specialized Australia served as our tour guide, taking us through the testing and prototype labs.
Specialized’s helmet lab
Mike Krynock, a mechanical engineer who works in Specialized’s helmet lab, took us through the process of designing and testing helmets – a process he described as arduous. It starts with sketches that are then modeled in clay. From there the model is cast and transferred into CAD design, from which a mold is cut and then re-cast. The design will go back and forth between these steps, while undergoing testing and further engineering, until it's finished and put into production. Krynock showed Specialized’s new Dissident carbon shelled downhill helmet in its steps from clay to the finished carbon product.

A clay model of the new Dissident full-face helmet
In addition to development, Specialized have a full-scale helmet test facility within the lab. Through the use of three test rigs and more than a dozen tests engineers can certify and further develop the company's helmets. Not only do Specialized run the tests in ambient conditions, they also freeze, super-heat (122˚F) and submerge the helmets before testing to draw the best possible correlations to real-world use.
Frame and component lab
Mark Schroder, Specialized’s director of engineering, took us through a smattering of the tests Specialized use to qualify and further develop their frames and components. He showed us six frame and component tests, which range from fatigue and strength tests to those that measure stiffness. “We test all of our components,” said Schroder, “ we test all of our frames and we test all of the brake systems we use.”

Schroder performs a full frame torsion stiffness test on a Venge aero road frame
Specialized also benchmark all of their competitors’ frames and forks by buying them and running them through a similar battery of stiffness, fatigue and strength tests. “It’s easy to be strong and lightweight,” said Schroder. But the key, he said, is to combine stiffness with comfort – an additional attribute that Speciaized test intensively for.
There are six different stiffness tests. “We use them to measure and analyze our prototypes," said Schroder. "We always start too light and creep up to make them just right." The stiffness, strength and fatigue tests are carried out for every model in every size, which Schroder says keeps the lab busy, to say the least.

In the test lab on the 'bottom out fatigue test machine' with a new 2012 M5 alloy Stumpjumper FSR Evo; the test runs 100,000 cycles with various weights depending on the intended use
Specialized prototype shop
Jon Sieber gave us a rundown of the prototype machine shop, which is connected to the test lab. This is where prototype frames and components are created to test concepts for new models and to accommodate Specialized's sponsored athletes. Sieber, who's worked in the lab for a year-and-a-half, said he enjoys getting to build frames for the best. However, the highest profile projects have been small parts that help get a star athlete in the proper position.
A highlight for Sieber was CNC machining three custom stems for Alberto Contador last year. When custom products like these stems are made, generally they’re used by the athlete to confirm the sizing and fit, then a stronger, lighter part is made at the standard production facility that makes the corresponding production parts.

The Haas VF3, Specialized's new $90,000 CNC mill
When we visited, Sieber was building a wheel test jig so that Specialized can conduct UCI wheel certification. Schroder said there are only two others that he knows of – at a certified Belgian test lab and at Trek’s Wisconsin factory. The latest piece of equipment came to the Specialized machine shop in February, in the form of a HAAS VF3 CNC machine. The US$88,000 machine (without shipping) took two months to assemble and set up, and is so big it required a hold to be cut in the wall to get it into the shop.

We must also mention that Specialized's headquarters is dog friendly
Take a walk through the rest of the Specialized HQ via our gallery.