Waldershof is a typical Bavarian town, backing on to the forest and littered with old architecture and shops that look as if they’ve not changed since the 90s.
Turn a few corners out of town though, and you’ll come across a low-key Cube sign pointing towards a massive plot of warehouse and office space, based literally a stone’s throw from where Cube first started in 1993.
Having originated in the space the size of a garage, Cube started as a small bike shop and distributor, but the founding team quickly decided they could do a better job designing bikes themselves – and from there things really kicked off.
Cube has had more than 10 percent year-on-year growth every year bar one, and in 2013 sold 412,000 bikes. Needless to say, the garage sized operation quickly outgrew its premises, and Cube had a new factory unit and office building designed and built.
The massive expansion of the company has meant that the office building has been extended multiple times – it has just been enlarged again – while the factory unit is still where the bikes are assembled. But a warehouse a five minute walk away is where the assembled bikes are stored.
Michael Prell, the chief bike designer and one of the three founders of the company, took us for a tour around the factory and offices, showing us just how challenging an operation it is being one of the biggest bike companies in Europe.
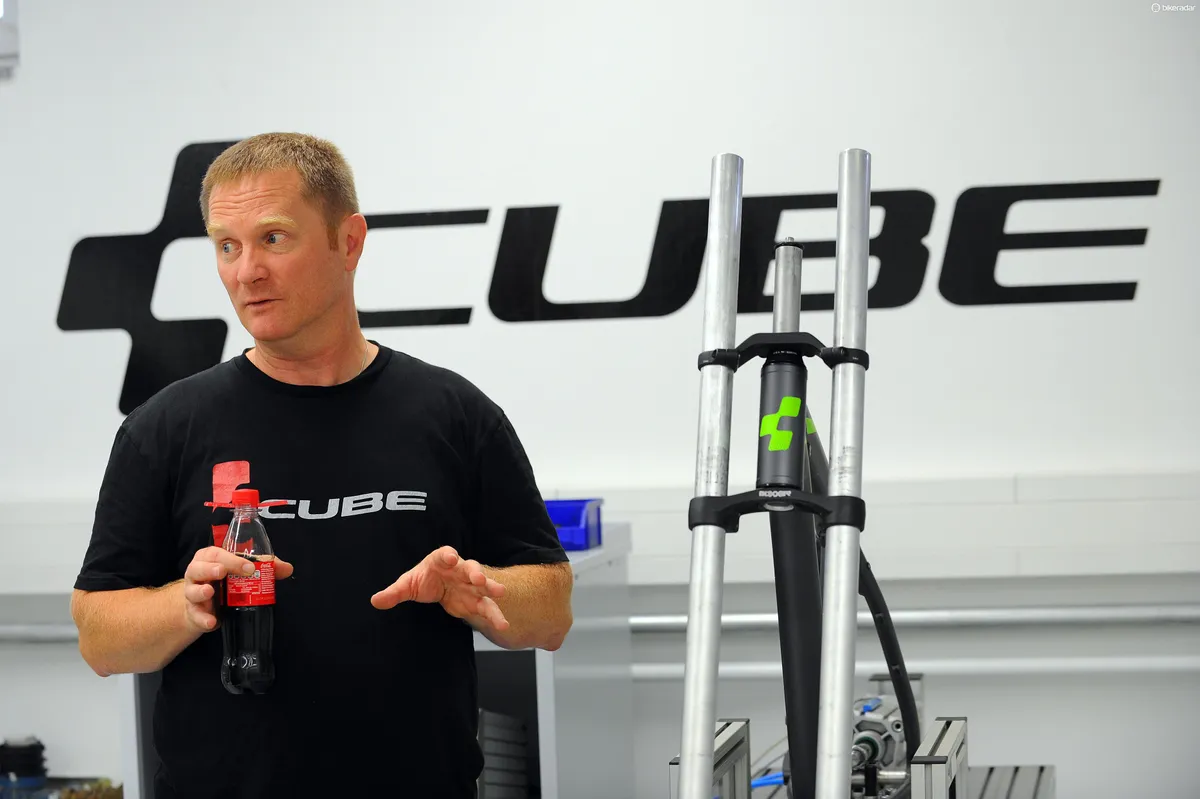
Michael Prell, one of Cube's founders and the head designer
Before any Cube goes into production it needs to be tested to make sure it’s strong enough and meets Cube’s standards, which exceed the basic benchmarks needed to sell the bikes by three times over. Cube does all its testing in house, and we were lucky enough to get a glimpse past the 'no camera' signs and have a good look in the testing department.
Every Cube frame gets a thorough workout, along with any components that haven’t been pushed to the level that Cube feels happy with. This essentially means there’s at least one machine running day and night, putting frames and components through their paces.
The front impact test is the big one that manufacturers generally look at. Cube is no exception, making sure that its bikes surpass the testing standard by three times. We could go on about this for ages, but it’s effectively the same as an average person riding into a wall at 45km/h, and we’re pretty sure doing that isn’t on anybody’s to-do list!

You might recognise some of the bikes on these test rigs. All of Cube's frame testing is done in-house
Once testing is complete, frames can go into production. Production frames will then, months later, arrive at the assembly line.
Carbon frames go through a quality control check before they’re assembled too, checking everything is within tolerance and good to go. It’s not a case of one in 10 either – literally every carbon frame is checked by an actual human being before being put onto the assembly line.
Every Cube bar some of the childrens bikes are assembled at the factory in Germany. When you take a moment to consider that nearly half a million bikes have travelled along the assembly line in Waldersof over the past year, it’s little wonder that the scale of the operation really has to be seen to be believed.
While frames are being bolted to seat post attachments on the long roof-mounted railway of an assembly line, over in the next building wheels are being produced ready to be bolted on later in the process. Scoping the sheer number of rims and tyres sat in the cavernous rubbery-smelling room hammers home the fact that thousands of wheels will be rolling out of the door every day. Once the wheels are assembled with disc rotors, cassettes and tyres attached, they’re put onto special trolleys and wheeled into the warehouse next door ready to be put onto the bikes.

Ever wondered how bikes are pre-built? Cube can turn over over a thousand in a day, with hundreds in progress at any one time
Before the frames get there, the assembly line takes them past stations to have the headset, fork and stem installed, then the frame and fork combo make their way into a massive room equipped with hundreds of bike building positions. Stopping at one of the stations, the bike gets the wheels, gearing, brakes and controls installed, and made ready to be individually packed into boxes ready to head to the warehouse and be shipped off.
Cube’s eBikes have a separate production line, because they’re only produced in small numbers and take a lot more time being assembled owing to their multitude of special parts and electronics that normal bikes don’t have.

The e-bikes have a separate assembly line as they take a lot more time and expertise to build perfectly
Walking around the factory took us the best part of a full day – and we didn’t even get as far as the warehouse! Sitting back in Cube’s glass walled main board room, we chatted about bikes to come and bike specs, especially for the British market, where we tend to prefer wider bars, shorter stems and single ring drivetrains.
“We simply couldn’t sell a 1x10 bike in Europe” explained Prell. “A lot of people are still sceptical about XX1” he went on, delivering a shock to our UK-centric ears.
We're lucky in that the designers and developers at Cube ride very similar setups to us Brits, so take us harder riders into account with every choice made on speccing up new frames. We can’t wait to get one of the new Stereo 140s back to test on our local trails.
BikeRadar US and Australia readers should note that Cube bikes are not available in their countries.